Many solutions have been proposed, but the actual application faces many major challenges, making the destination still far away. Green steel – The steel industry's destination in the Net Zero race
Steelmaking is an industry that plays an important role in the world economy, but is also one of the industries that emits the most greenhouse gases. According to estimates by organizations around the world, producing 1 ton of steel will emit 1.8 - 2 tons of CO2 gas.
According to the World Steel Association, currently, traditional steel production emits about 3.6 billion tons of CO2 per year and accounts for 9% of global emissions. Meanwhile, Bloomberg estimates that world steel demand from now to 2050 is forecast to increase by about 20% compared to the present.
Therefore, in the race to net zero emissions by 2050, steel manufacturing enterprises in the world and Vietnam in particular are still looking for solutions for products called "green steel".
Green steel refers to the concept of steelmaking using advanced technologies and “green” materials to minimize CO2 emissions during the production process.
In addition, recognition of a "green steel" product requires that both the direct steel production process and the production process of raw materials and input fuels (such as electricity and gas) are emission-free.
This concept has appeared in the world since 2021 when steel producing countries began to consider solutions to meet emission requirements, especially in Europe. In Vietnam, this product received more attention after the Environmental Protection Law was issued in 2020, effective from January 1, 2022.
One of the most known solutions in making green steel is using green hydrogen gas (Hydrogen Breakthrough Ironmaking Technology, also known as Hybrit).
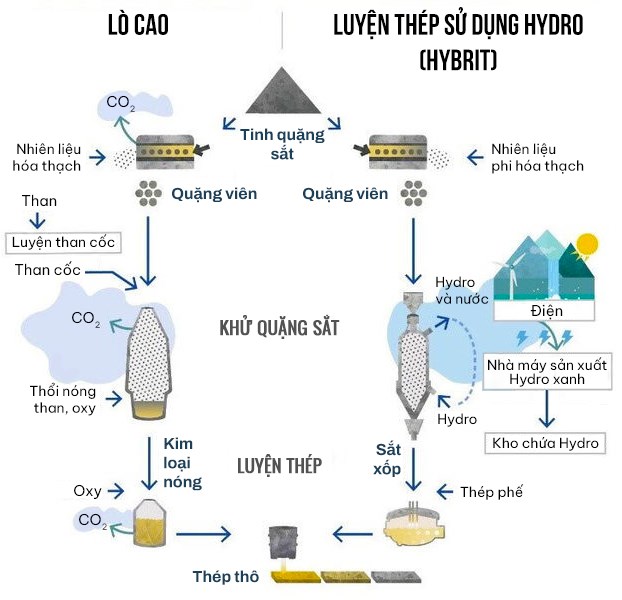
Photo: Australia Mining Monthly
Unlike the traditional steelmaking method of heating iron ore with coke in a blast furnace, with the Hybrid method, factories will use green hydrogen gas to melt iron ore.
The quality of input iron ore for furnaces using hydrogen gas requires over 67% Fe and few impurities, while current blast furnaces mainly use ore of 62% Fe or lower quality.
If green hydrogen production uses renewable electricity, the amount of gas emitted is reduced by up to 98% compared to traditional steelmaking methods.
The second method uses a biomass incinerator. The fuel for this furnace is biogas (CO; H2; CH4,...) produced by pyrolysis reaction in an anaerobic environment of biomass materials such as wood, rice husk, agricultural by-products Karma,...
In addition to the above two steel production methods, steel factories can consider buying carbon credits or burying CO2 gas, planting more trees like other industries.
The "transformation" is not easy
In fact, having a successful "transformation" in the steel industry is not easy. Changing technology means spending a large amount of money. At the same time, the supply of input materials for these new technologies also needs to be large enough and affordable.
For example, with the method of using hydrogen gas, there are two big questions: whether there is enough supply of high-quality gas and iron ore and whether the price is attractive enough to balance the profits of the business and consumer benefits?
According to data from the US National Mineral Information Center, the world's supply of iron ore with quality over 67% only accounts for about 10%, the rest is mostly iron ore of 62% or lower. Meanwhile, world steel demand in 2022 is about 1.8 billion tons. Thus, if green steel is produced with technology using hydrogen gas, it can only yield about 180 million tons.
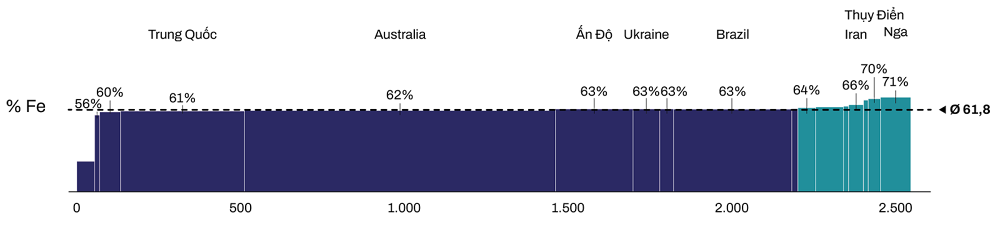
Fe content in global iron ore production in 2021 (Unit: million tons. Data: US National Mineral Information Center)
Furthermore, producing hydrogen fuel requires a large amount of electricity consumption, but if coal power is used, it is still counted as having indirect carbon emissions. In addition, in the context of unstable electricity supply during peak summer periods, green hydrogen production is an even more difficult problem.
According to steel industry experts, currently hydrogen steel production technology in the world is still in the testing stage and the cost is very expensive.
In a report published in May, Morgan Stanley Bank said the investment required to decarbonize the European steel industry (using green hydrogen solutions) could exceed $1,200 per ton of capacity. For a steel company that produces an average of 5 million tons per year, that equates to about $6 billion in capital expenditures. It is estimated that switching to hydrogen steel production in Europe requires about 130 billion USD, the region's electricity output needs to increase by 8% and green hydrogen capacity must be more than 5 million tons.
Similar problems are being raised with the method of producing steel using biomass gas because it requires a large amount of gas supply. This poses a challenge in classifying waste and by-products because it takes a lot of time.
With the carbon burial solution, according to Dr. Luong Quang Huy, Head of the Department of Greenhouse Gas Emissions Mitigation and Ozone Layer Protection, currently only a few countries in the world apply it at a not cheap cost. - 160 USD/ton CO2. Thus, to produce 1 ton of steel, businesses have to spend 300 - 320 USD (equivalent to nearly 7 million VND) for carbon treatment. However, that is not the final number because there are many other variables, especially if applied in Vietnam without experience in this field.
As for the solution of buying carbon credits, Vietnam is still in the process of building a legal framework. Accordingly, in the period 2022 - 2027, Vietnam will focus on building regulatory systems and policies to create a foundation for the market to operate as well as establishing and organizing pilot operation of a carbon credit exchange, aiming to officially operate the carbon credit exchange in 2028.
"We are also interested in the option of buying carbon credits, but we still have to wait for the exchange to be officially operated," Hoa Phat representative shared.
Besides production problems, steel companies also have to face whether customers are willing to pay much higher prices than conventional steel to use green steel. This probably depends a lot on environmental protection awareness and the customer's budget.
Typically, in the US and EU markets, the level of willingness to spend money on green steel is very different. According to Fastmarkets, in Europe, the demand for green steel is much higher than in the US. European steel companies have begun to pursue this path - selling green steel at higher prices.
On the contrary, in the US market, buyers are currently not interested in paying more for green steel than in European countries. This lack of enthusiasm is partly due to the fact that last year, steel prices in North America and other American markets continuously reached record levels. Rising steel prices in 2022 have caused some US buyers to pay four times more than in 2019-2020.
What are Vietnamese steel businesses doing to adapt?
Talking to us, Mr. Nghiem Xuan Da, Chairman of the Vietnam Steel Association and General Director of Vietnam Steel Corporation, commented: "It seems that achieving the goal of greening the steel industry by 2050 is still possible. still quite far away. The investment cost of green steel production can be 4-5 times more expensive than normal."
However, according to him, this is an inevitable trend that businesses need to pursue because the world is setting strict standards on emissions, especially in Europe.
At the current stage, steel businesses are gradually adapting and preparing the first steps for the greening process through optimizing production processes and applying circular economy.
“Current technology has not greatly reduced the use of coal in blast furnaces. Therefore, Hoa Phat currently deflates by optimizing production, taking advantage of heat and excess gas to generate electricity. Currently, we are 80% self-sufficient in power sources using renewable energy and utilizing excess heat and gas. Some other by-products such as slag from blast furnaces are crushed for use in the cement industry. When using this by-product, the cement industry eliminates one clinker burning step that causes emissions. In addition, we also circulate water use, not discharging it into the environment," said Mr. Nguyen Viet Thang, General Director of Hoa Phat Group.
A representative of Vietnam's largest steel manufacturing company added that this unit is also working with a number of organizations to consider carbon burial options if all used solutions are not optimal in terms of efficiency.
Mr. Pham Cong Thao, Deputy General Director of Vietnam Steel Corporation, said the company is also planning to invest in more technology to take advantage of heat and residual gas emitted from blast furnaces to produce electricity. In addition, the company uses electric furnace (EAF) technology, which reduces emissions by about 50% compared to blast furnace technology at about 1 ton of CO2 for 1 ton of steel.
In the future, Mr. Thao hopes that with Vietnam's renewable electricity growing strongly along with new technologies that help make the cost of producing green steel with Hydrogen cheaper, consumers will easily accept the selling price of steel. green.
“2050 is the destination of green transformation for the steel industry in particular. But is it possible and how? is still a question that businesses seek answers to because there are too many variables. But this is an inevitable trend and businesses need to learn how to adapt," said a representative of a large steel company in the industry.
Vietnambiz